Understanding Injection Mold Manufacturing
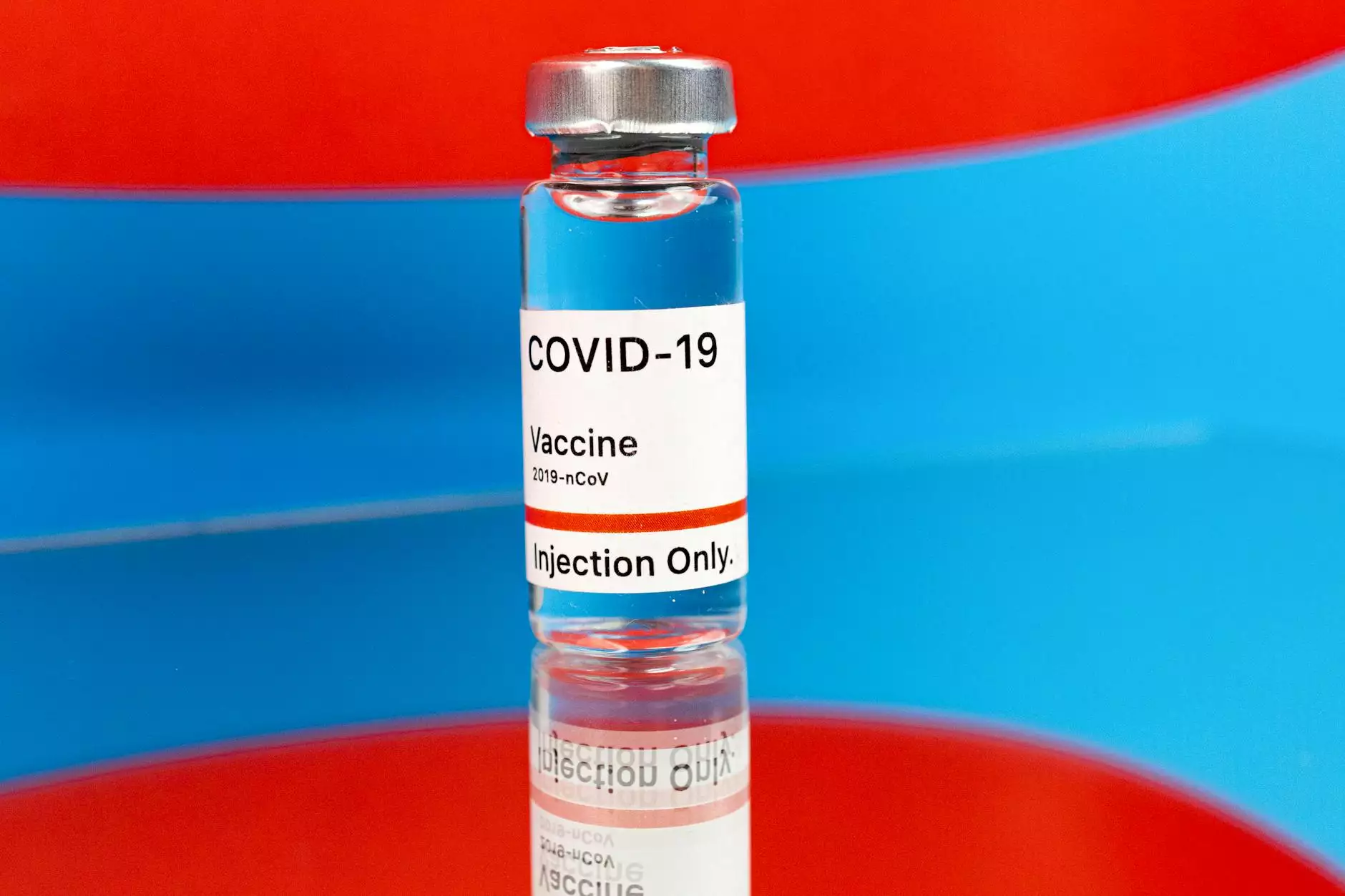
Injection mold manufacturing is a cornerstone of modern production techniques, playing a crucial role in various industries, especially in the realm of metal fabrication. This process not only enables the creation of intricate designs but also ensures high efficiency and precision in manufacturing. In this comprehensive guide, we will delve into the aspects of injection mold manufacturing, exploring its advantages, the techniques involved, and its impact on the metal fabrication sector.
What is Injection Mold Manufacturing?
Injection mold manufacturing is a process where molten material is injected into a mold cavity to produce parts and components. This technique is widely used for creating complex shapes and designs that are difficult or impossible to achieve with other manufacturing methods.
The molds used in this process are typically made from durable materials such as steel or aluminum, enabling the production of high-quality and long-lasting parts. The injection process is ideal for mass production, making it a preferred choice for manufacturers in various sectors, including automotive, consumer goods, and healthcare.
The Process of Injection Mold Manufacturing
Understanding the process of injection mold manufacturing is essential for appreciating its significance. Here are the main steps involved in the process:
- Designing the Mold: The first step involves creating a detailed design of the mold based on the desired product specifications. This stage usually employs CAD (Computer-Aided Design) software to produce a precise model that can be manufactured.
- Creating the Mold: Once the design is finalized, the mold is fabricated using high-quality materials. The manufacturing of the mold is a critical phase that requires attention to detail to ensure accuracy and longevity.
- Injection: Molten material, often thermoplastics or thermosets, is injected into the mold under high pressure. This phase demands precise control over temperature and pressure to achieve the desired material properties.
- Cooling: After the injection, the mold is cooled to solidify the material. This cooling time impacts the cycle time of production and must be optimized for efficiency.
- Demolding: Once solidified, the mold is opened, and the finished product is removed. Any necessary post-processing can then be performed to enhance the final product's quality.
Benefits of Injection Mold Manufacturing
Injection mold manufacturing offers numerous advantages that make it an attractive option for businesses. The benefits include:
- High Efficiency: Once the mold is created, the injection process allows for rapid production and short cycle times, making it suitable for large-volume manufacturing.
- Precision and Accuracy: The process allows for the production of highly detailed parts with tight tolerances, which is particularly important in industries such as aerospace and automotive.
- Material Versatility: A wide range of materials can be used in injection mold manufacturing, including various plastics, metals, and composites, making it adaptable to different applications.
- Cost-Effectiveness: While initial mold manufacturing may be costly, the long-term production efficiency and low per-unit costs make it economically viable for mass production.
- Customization: Modifications can be made easily during the designing stage, allowing manufacturers to customize products to meet specific customer needs.
Injection Mold Manufacturing and Metal Fabricators
Injection mold manufacturing is particularly significant for metal fabricators, as it allows for the production of intricate metal parts that require precision and durability. The integration of injection molding techniques in metal fabrication has revolutionized the way products are developed and produced.
Metal fabricators who employ injection mold manufacturing can achieve better design flexibility, optimize production processes, and reduce waste. By utilizing advanced technology in injection molding, these fabricators can ensure high-quality outputs while meeting rigorous industry standards.
Collaboration Between Injection Mold Manufacturers and Metal Fabricators
For optimal results, collaboration between injection mold manufacturers and metal fabricators is essential. This partnership can lead to:
- Innovative Solutions: Joint efforts can foster innovative manufacturing solutions that enhance product functionality and market competitiveness.
- Improved Prototyping: Fast prototyping capabilities allow for rapid testing and iteration, leading to better product development and reduced time-to-market.
- Quality Control: This collaboration can enhance quality control processes, ensuring that both the mold and the fabricated parts meet the necessary standards.
Technology in Injection Mold Manufacturing
The evolution of technology has significantly impacted injection mold manufacturing, leading to advancements that enhance efficiency and output quality. Key technological innovations include:
- 3D Printing: Rapid prototyping with 3D printing technologies can expedite the design and testing phases of molds, allowing manufacturers to iterate designs quickly.
- Injection Molding Simulation: Advanced simulation software enables manufacturers to visualize the molding process, optimizing the design before actual production begins.
- Smart Manufacturing: The integration of IoT (Internet of Things) devices in manufacturing processes allows for real-time monitoring and adjustments, improving efficiency and reducing downtime.
Future Trends in Injection Mold Manufacturing
The future of injection mold manufacturing looks promising, driven by technological advancements and increased demand for customized solutions. Some trends to watch include:
- Sustainability: There is a growing emphasis on eco-friendly practices within the manufacturing sector, leading to the development of recyclable materials and sustainable production processes.
- Automation: The rise of automation in injection molding processes is set to enhance productivity and further reduce labor costs.
- Continuous Improvement Processes: Manufacturers are increasingly adopting methodologies like Lean Manufacturing and Six Sigma to continuously improve efficiency and minimize waste.
Conclusion: The Integral Role of Injection Mold Manufacturing
Injection mold manufacturing stands as a vital process in the realm of metal fabrication and beyond. Its ability to produce complex, high-quality parts efficiently makes it indispensable for various industries. As technology continues to advance and sustainability becomes a priority, businesses in this field must adapt and evolve to maintain their competitive edge.
Investing in advanced injection mold manufacturing techniques not only improves production capabilities but also enhances product quality and customer satisfaction. Companies like Deep Mould are leading the way in this innovation, ensuring that they remain at the forefront of the industry.
Call to Action
For businesses looking to leverage the benefits of injection mold manufacturing, partnering with experienced professionals and staying informed about the latest trends is essential. Explore the opportunities that injection mold manufacturing can provide for your production needs today!