The Essential Role of a **Bottle Label Applicator** in Modern Business Operations
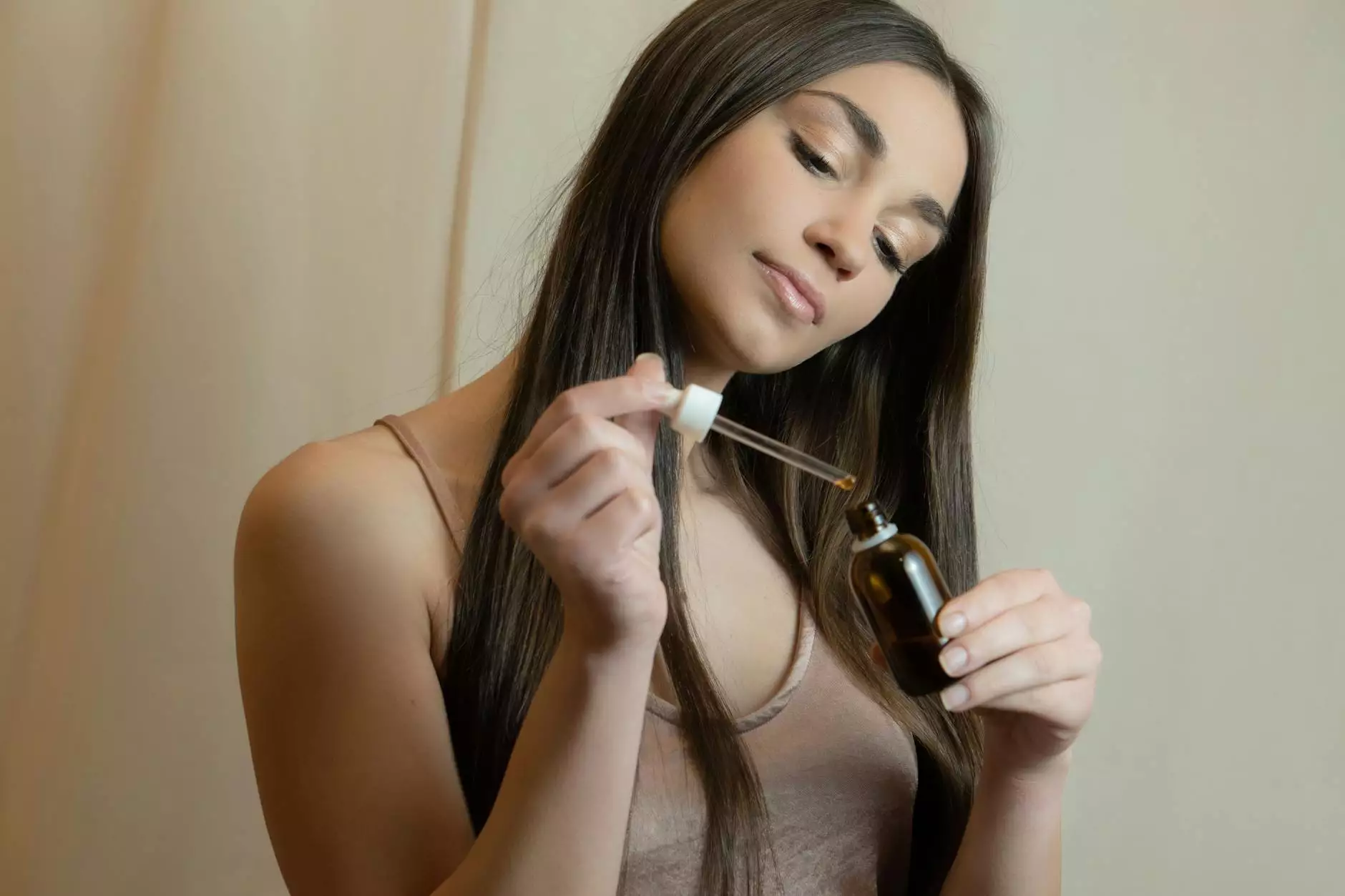
The world of business is continuously evolving, and with it comes the need for efficient operations that not only save time but also enhance productivity. A key component in streamlining production processes, particularly in industries such as food and beverage, cosmetics, and pharmaceuticals, is the bottle label applicator. This article delves deeply into the various aspects of bottle label applicators, examining their functionality, benefits, and why businesses should consider integrating them into their operations.
Understanding the Bottle Label Applicator
A bottle label applicator is a device designed for applying labels to bottles in a fast and precise manner. These machines can vary in complexity, from simple manual models to sophisticated automatic systems capable of handling various bottle sizes and shapes. By automating the labeling process, businesses can achieve greater consistency, speed, and accuracy in their packaging operations. Let’s explore the core components that contribute to its effectiveness.
Core Components of a Bottle Label Applicator
- Label Feed System: This system controls the delivery of labels to the applicator, ensuring there are no jams or misalignments during production.
- Labeling Head: The heart of the applicator, the labeling head is responsible for applying the label onto the bottle. This part can be adjusted to accommodate different bottle sizes.
- Control Panel: Typically featuring a user-friendly interface, the control panel allows operators to set parameters, such as the speed of application and the placement of labels.
- Conveyor System: Many bottle label applicators include a conveyor system that moves bottles through the labeling process, increasing efficiency.
- Integration Features: Modern applicators often provide compatibility with other production equipment, simplifying operational workflows.
Benefits of Using a Bottle Label Applicator
Investing in a bottle label applicator can yield numerous advantages for your business. Here are some of the most significant benefits:
Increased Production Efficiency
Labeling bottles manually can be a time-consuming and cumbersome task. By implementing a bottle label applicator, your production line can see a significant boost in efficiency. These machines are designed to work at high speeds, enabling your team to handle larger batches of products in less time, ultimately increasing throughput.
Enhanced Label Accuracy
One of the most critical aspects of packaging is the accuracy of label placement. A bottle label applicator ensures that labels are applied precisely every time, minimizing the risk of errors that can occur with manual application. This precision is crucial for maintaining brand integrity and complying with regulatory requirements.
Cost-Effective Solution
Although a bottle label applicator requires an initial investment, the long-term savings are notable. Reduced labor costs, decreased material waste due to misaligned labels, and faster processing times contribute to a lower overall cost per unit. This investment can lead to greater profitability over time.
Improved Workplace Safety
Automating the labeling process helps reduce the likelihood of workplace accidents. Manual labeling often involves repetitive motions that can lead to strain injuries. By employing a bottle label applicator, businesses can create a safer work environment while enhancing efficiency.
Versatility Across Industries
Whether you are in the food and beverage sector, cosmetics, or pharmaceuticals, a bottle label applicator can be tailored to meet your specific needs. With the ability to handle various sizes and shapes of bottles, it provides versatility that can accommodate a wide range of products.
Choosing the Right Bottle Label Applicator for Your Business
When considering a bottle label applicator, it is essential to evaluate your business needs and the specific features that will benefit you the most. Here are some critical factors to keep in mind:
Production Volume
Assessing your production volume is vital in selecting the right applicator. For businesses with high output, an automatic applicator may be necessary. In contrast, lower volume operations might find a semi-automatic model sufficient.
Type of Labels
Understanding the types of labels you will be using is crucial. Some applicators are designed for pressure-sensitive labels, while others can handle shrink sleeves or wrap-around labels. Ensure the applicator you choose is compatible with your labeling materials.
Space Considerations
Space constraints in your facility might limit your options. Consider the dimensions and layout of the area where the applicator will be housed. Compact models may be more suitable for smaller operations, while larger automatic systems may require dedicated spaces.
Budget
Establish a budget, considering both the initial purchase price and potential maintenance costs. Remember that while cheaper models may be enticing, investing in a reliable and high-quality bottle label applicator can pay off in the long run.
How to Integrate a Bottle Label Applicator Into Your Production Line
Successfully integrating a bottle label applicator into your production line requires careful planning and consideration. Here are steps to ensure a smooth transition:
1. Assess Current Processes
Review your existing labeling process to identify inefficiencies and areas for improvement. This assessment will help you understand how best to implement the new system.
2. Choose the Right Model
Based on your assessment, select a model that fits your production needs, taking into account factors like speed and label type.
3. Train Your Team
Proper training is crucial for ensuring that your team can operate the new machine effectively. Conduct training sessions and provide manuals to assist staff in understanding the applicator's features.
4. Monitor Performance
After implementation, monitor the applicator's performance regularly. This includes checking for any issues in label application and addressing them promptly to maintain efficiency.
5. Solicit Feedback
Gather feedback from your team to identify any additional training needs or adjustments that could further optimize the labeling process.
Conclusion
In conclusion, a bottle label applicator can be a game-changer for businesses that depend on efficient, accurate, and reliable labeling. With numerous models available tailored to various production needs, it’s crucial to invest wisely after assessing your current and future requirements.
With increased production efficiency, reduced costs, enhanced label accuracy, and improved safety, the right bottle label applicator not only streamlines operations but also solidifies your company’s reputation for quality. As consumers demand transparency and quality in packaging, investing in this technology could be one of the best decisions for your business.
For more information on quality bottle label applicators and other packaging solutions, visit omegabrand.com today!